Eliminating Waste: Creating Efficiency in Nonprofit and Healthcare Organizations
Author:
Jim McGuirk

In the past three months, there’s been considerable discussion about creating efficiencies in both government and private organizations. While cost-cutting is often the default response to challenging times, simply reducing headcount without understanding who delivers the most value can actually decrease overall efficiency. This is especially true for mission-driven organizations like nonprofits and healthcare institutions where staff are typically overworked. While budget constraints often lead to reducing staff without proper analysis, this approach can undermine both mission fulfillment and service quality. For organizations where every resource directly impacts beneficiary outcomes or patient care, a more strategic approach is essential.
Lean Six Sigma: A Mission-Aligned Approach to Efficiency
Lean Six Sigma (LSS) offers a systematic alternative to arbitrary cuts that respects the unique purpose of mission-driven organizations. Originally developed in manufacturing settings by Toyota, Motorola, and GE, these methodologies have been successfully adapted for healthcare systems, community organizations, and other service-focused entities.
The core LSS principle remains powerful for mission-driven contexts: everything is a process, and every process can be improved. True efficiency comes from eliminating waste—any step that doesn’t add value to your beneficiaries, patients, or community stakeholders.
DOWNTIME: The 8 Wastes Impacting Your Mission Effectiveness
Waste manifests differently in nonprofit and healthcare settings but follows similar patterns. The LSS acronym DOWNTIME helps identify these barriers to mission fulfillment:
D – Defects: Outputs requiring correction (documentation errors, service quality issues, clinical mistakes requiring remediation)
O – Overproduction: Creating more than needed (excessive paperwork for clients/patients, redundant reporting to funders)
W – Waiting: Delays in service delivery (appointment wait times, funding approval bottlenecks, client intake delays)
N – Non-utilized Talent: Underutilizing staff and volunteer skills (common in hierarchical healthcare systems and nonprofit structures where frontline knowledge goes untapped)
T – Transportation: Unnecessary movement of resources, information, or patients (inefficient referral processes, multiple care locations)
I – Inventory: Excess supplies or backlogged cases (medical supplies beyond needs, unprocessed client applications)
M – Motion: Unnecessary movement of caregivers or staff (poor clinic layout, inefficient community outreach routing)
E – Extra Processing: Work beyond what creates beneficiary/patient value (redundant documentation, excessive compliance activities not required by funders/regulators)
Implementation That Preserves Mission Focus
What makes LSS particularly valuable for mission-driven organizations is its collaborative, bottom-up approach. Rather than imposing changes that might compromise care or services, it engages those who understand both processes and mission impact—your frontline staff, caregivers, and even clients or patients when appropriate.
For resource-constrained organizations, Rapid Process Improvement (RPI) can deliver quick wins without major investment. By focusing on targeted improvements with short timeframes, you can create momentum while building internal capability and demonstrating value to funders or governing boards.
The Mission-Critical Results
Organizations that focus on eliminating waste rather than arbitrary cuts typically achieve:
- Increased service capacity with existing resources
- Higher quality care or program outcomes
- Greater staff engagement and reduced burnout
- More sustainable financial models
- Enhanced ability to demonstrate stewardship to donors and funders
- A culture of continuous improvement focused on mission fulfillment
During challenging funding environments, the path of least resistance is often across-the-board cuts. However, the mission-driven organizations that emerge stronger are those that use constraints as a catalyst to enhance their impact by systematically eliminating waste.
What's Next?
Process mapping is the first step in identifying waste in your nonprofit or healthcare organization. In my next article, I’ll show you how to visualize your service delivery or patient care processes to make waste visible and targetable in ways that protect your core mission.
Have you implemented Lean Six Sigma in your nonprofit or healthcare organization? What forms of waste have been most challenging to address while maintaining service quality? Share your experiences in the comments below.
Connect with me for more insights on creating sustainable efficiency that enhances rather than compromises your mission.
Jim McGuirk has a PhD in Counseling Psychology and a Black Belt in Lean Six Sigma. Jim was CEO at Astor Services for Children & Families for 17 years.
Position Your Organization for the Future
Let us know how CCMS Partners can support your organization
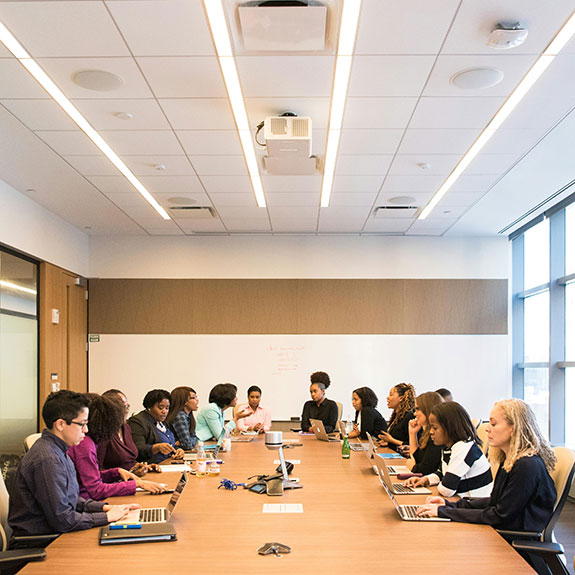